What is the Safe Torque Off (STO) functionality?
What are the main advantages of the STO Safe Torque Off for drives for stepper motors and brushless motors?
The Safe Torque Off (STO) function is a safety function integrated in several Ever Elettronica digital servo drives for stepper motors or brushless.
The Safe Torque Off STO is a safety input on the drives that, through a certified circuit, cut off the power supply to the motor, thus removing torque and preventing it from restarting unexpectedly, compromising safety. The function of Safe Torque Off STO is an extremely safe stop function: compared to a normal enable input, it does not pass through a microprocessor but acts directly on the electronic circuit that powers the motor, ensuring the stop and leaving the drive’s logic on.
Safe Torque Off STO allows servo motors, stepper and brushless, to interrupt power without damaging the driver or the surrounding motors parts.
That’s why Safe Torque Off STO, which is the safety feature “par excellence” for most servo stepper and brushless drives manufacturers, can be found in different industrial applications, from conveyor belts to robotics.
How the Safe Torque Off STO works?
Safe Torque Off STO is a redundant input that and disabled, it is supplied with a 24 Vdc.
Once the Safe Torque Off STO is enabled, through the Safety Torque Off STO switch or via a safety unit, a certified circuit removes the supply voltage from the transistors that regulate servo motor current.
After the stop, the motor stops by inertia.
Ever Elettronica drives for stepper motors and brushless motors recognize the enabling of the Safe Torque Off STO and, while remaining active in the logic, they send the security protection to an external PLC via Ethercat, Profinet, Canopen or Modbus TCP/IP fieldbuses.
How can you restart the servomotor after the stop?
The only way to restart a servo motor, after activating the safety function Safe Torque Off STO is to disable the safety input, bringing the voltage of 24 Vdc back to the terminals of the 2 security inputs.
Which are the main advantages of the STO Safe Torque Off for the drives for stepper motors and brushless motors?
The main advantages of the Safe Torque Off STO for the drives for stepper and brushless motors are:
- Increased machine safety
- Reduced costs and time for the machines certification
- Reduction of safety devices on the machine
- Wiring simplification with relative reduction of costs
Drives with integrated STO Safe Torque Off function do not require additional relays to interrupt the power supply to the drives, because the power supply is directly interrupted by the STO Safe Torque Off input.
Safety connection without STO Safe Torque Off
.png)
Safety connection with STO Safe Torque Off
.png)
Figure 1: Safety with and without STO Safe Torque Off
Safety standards
The STO function has to be compliant with a specific safety standard. The following table shows the safety indices for SIL (Safety Integrity Level) and PL (Performance Level).
The Stop categories are defined by the IEC 60204-1 certified standards for machine safety:
The Stop categories are defined by the IEC 60204-1 certified standards for machine safety: |
Stop Category 0 | Stop by immediate removal of power to the drives and motor |
Stop Category 1 | Controlled stop with power, with power removal once the stop has occurred |
Stop Category 2 | controlled stop without power failure |
The Safe Torque Off STO function of Ever Elettronica drives refers to the Stop Category 0, as per IEC 60204-1 regulation.
The Stop Category 0 provides stopping by immediate removal of power to the driver and motor.
In order to guarantee the STO Safe Torque Off functions, the STO Safe Torque Off has to be certified by an authorized body.
The circuits on the Ever Elettronica drives for the STO Safe Torque Off function are certified by the internationally recognized UL International.
Thanks to the collaboration with the UL Body, Ever Elettronica offers stepper drives, stepper motors, brushless drives and brushless motors UL Recognized.
Ever Elettronica UL recognized products perfectly match the needs to export on the United States and Canadian markets.
To find out more about our UL Recognized motors and drives, click on the link below
Our UL Certified products
Specifications of STO Safe Torque Off inputs in Ever Electronic drives
The standard applied for STO Safe Torque Off circuits in Ever Elettronica drives is EN/ISO 13849-1 and the safety level is SIL3/Ple.
The STO Safe Torque Off circuit is certified by an independent body, UL International, which has performed the certification tests issuing a certificate of conformity.
The following table shows the certification values of the Safe Torque Off STO inputs, divided according to the different families of drives:
SW5A9052, SW5A5080, AW5A91K5 Drives Series
Safety function | STO | Safe Torque Off
|
Category | 4 | In accordance with EN ISO 13849-1 |
Performance Level | PLe | In accordance with EN ISO 13849-1 |
Safety Integrity Level | SIL3 | In accordance with EN ISO 13849-1 table 3 |
DCavg [%] | 99 | Average Diagnostic Coverage |
PFHD [1/h] | 6,44 x 10-9 | Probability of dangerous failure per hour |
MTTFD [Years] | 368 | Mean time to dangerous failure |
Mission Time [Years] | 20 | In accordance EN ISO 13849-1 |
SW5A9030, AW5A9750, AW5A6750 Drives Series
Safety function | STO | Safe Torque Off
|
Category | 4 | In accordance with EN ISO 13849-1 |
Performance Level | PLe | In accordance with EN ISO 13849-1 |
Safety Integrity Level | SIL3 | In accordance with EN ISO 13849-1 table 3 |
DCavg [%] | 99 | Average Diagnostic Coverage |
PFHD [1/h] | 7,04 x 10-9 | Probability of dangerous failure per hour |
MTTFD [Years] | 351 | Mean time to dangerous failure |
Mission Time [Years] | 20 | In accordance with EN ISO 13849-1 |
Description of the operation of the SIL3/Ple STO Safe Torque Off inputs
The STO Safe Torque Off function is implemented on 2 channels (STO 1 and STO 2) through a S1 safety switch, so the control voltage ( 24 VDC) is disabled on both STO 1 and STO 2 inputs
(figure 2).
Both inputs must be switched simultaneously and always have the same voltage value at 24vdc.
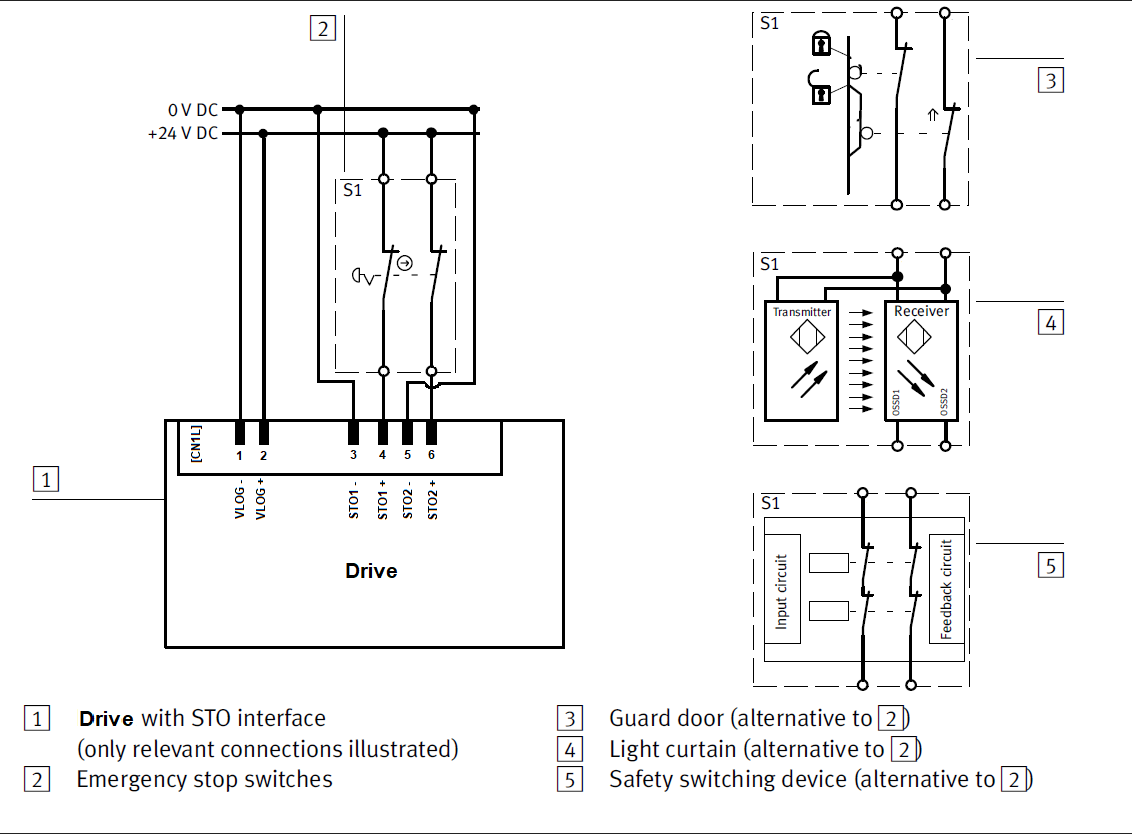
If there is a different value between the two inputs, the hardware diagnostic circuit disables the power supply of the power stage, informing the microcontroller of the presence of an alarm that will be displayed on the display and signalled by the FAULT output.
Driver reaction to the STO Safe Torque Off enabling
• Driver behaviour with moving motor
For the intrinsic operation of the STO Safe Torque Off / SIL3 input, the motor is not stopped by a deceleration ramp but will continue to move by inertia or external forces until its physical stop.
• Driver behaviour with the motor stopped
With the motor stopped the driver will not control the motor, leaving it free to move under external forces.
How is the Safe Torque Off STO SIL3 circuit realized?
Figure 3 exemplifies the design that implements the Safe Torque Off (STO) functionality using double-channel isolated STO signals that enable or disable the power supply (VCC) to the integrated circuit (IC) gate-driver via load switches that provide a redundant option. To ensure an high degree of security, two redundant and independent inputs are implemented in the hardware.
The Safe Torque Off STO circuit is designed so that a failure at one control input does not affect the other’s ability to prevent the motor from starting (single fault tolerance).
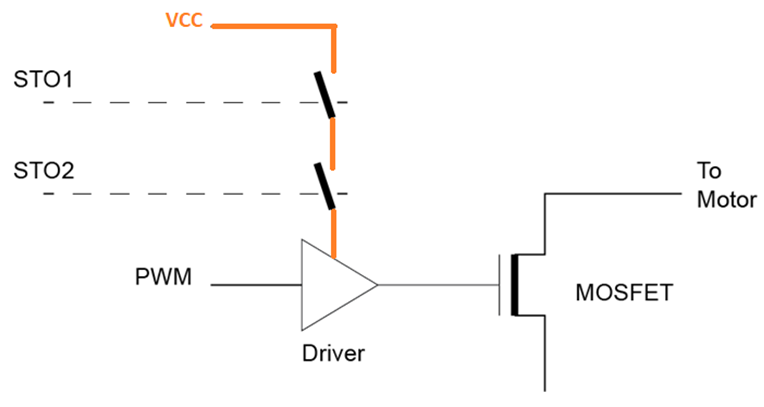
Figure 3: how the Safe Torque Off STO/ SIL3 is made in Ever Elettronica drives
This design implements Safe Torque Off (STO) functionalities using isolated dual channel STO signals that enable or disable power (VDC) to the gate-driver integrated circuit (IC) via load switches that provide a redundant option. To ensure an high safety degree, two independent STO Safe Torque Off control channels are implemented in the hardware. The STO Safe Torque Off circuit is designed so that a fault in one control channel does not affect the ability of the other channel to prevent the driver from starting (single fault tolerance).
This implementation of the Safe Torque Off STO functionality works with negative logic, deactivating the power stage by default.
To activate the power stage, and thus allowing motor’s operation, both differential inputs must be powered.
These inputs activate two opto-couplers that enable the power supply of the Gate-Drivers which control the power stage. If the Safe Torque Off STO inputs are not powered, the power stage transistors are switched off too because the Gate-Drivers which control the motor’s bridge will not have power supply.